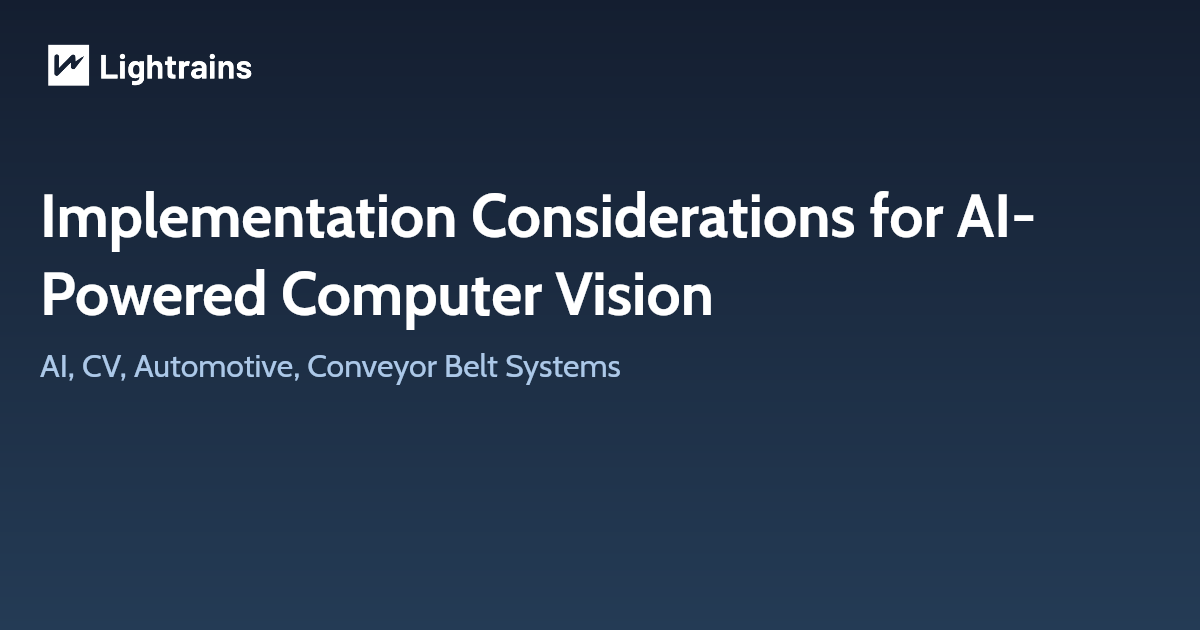
Implementing AI-powered computer vision systems in automotive manufacturing involves several critical considerations to ensure the technology not only integrates seamlessly with existing operations but also delivers the intended improvements in efficiency, quality, and safety.
1. Camera Selection and Placement
Resolution and Sensitivity: High-resolution cameras with excellent sensitivity are essential for capturing detailed images, even in varying lighting conditions typical in automotive factories.
Field of View and Placement: Cameras should have a wide field of view and be strategically placed to cover the entire conveyor belt, ensuring no component goes uninspected.
Durability and Maintenance: Given the harsh industrial environment, cameras must be durable and easy to maintain.
2. Image Processing Unit (IPU)
Key computer vision techniques such as edge detection, feature matching, and image segmentation are commonly used to recognize shapes, detect surface defects, and ensure products meet quality standards. This automated process minimizes human error and increases detection rates, especially in high-speed production environments. Real-Time Object Detection with Computer Vision
Processing Power: The IPU should have sufficient processing power to analyze images in real-time, preventing bottlenecks in the production line.
Software Compatibility: Ensure the IPU is compatible with the latest image processing and machine learning software, allowing for updates and upgrades.
3. Integration with Manufacturing Systems
Seamless Connectivity: The system should integrate seamlessly with existing manufacturing execution systems (MES) and enterprise resource planning (ERP) systems for streamlined operations.
Data Handling: Efficient handling of the large volumes of data generated by the cameras is crucial. This includes secure storage, quick retrieval, and effective data analysis capabilities.
4. Training and User Adoption
Operator Training: Comprehensive training for operators is crucial for them to understand how to interact with the new system and interpret its outputs.
Change Management: Implementing such advanced technology may require a cultural shift within the organization. Effective change management strategies will be essential for smooth adoption.
5. Maintenance and Support
Regular Maintenance: Scheduled maintenance of the cameras and the IPU is necessary to ensure consistent performance.
Technical Support: Reliable technical support from the system provider is crucial for troubleshooting and resolving any issues promptly.
6. Scalability and Future-Proofing
Scalability: The system should be scalable to accommodate future expansion of the production line or integration with other technologies.
Future-Proofing: Consider future technological advancements and ensure that the system can be updated or upgraded without significant overhauls.
7. Regulatory Compliance and Safety
Compliance with Standards: Ensure that the system complies with industry standards and regulations, particularly those related to safety and data security.
Safety Protocols: Incorporate safety protocols to protect workers from any potential hazards introduced by the new system.
8. Financial Considerations
Cost-Benefit Analysis: Conduct a thorough analysis to understand the return on investment, considering not just the initial costs but also long-term benefits in terms of increased efficiency and reduced waste.
Budgeting for Upgrades: Allocate budget not just for the initial setup but also for future upgrades and maintenance.
By meticulously addressing these considerations, automotive manufacturers can effectively leverage AI-powered computer vision systems to enhance the efficiency, quality, and safety of their conveyor belt operations, thereby gaining a competitive edge in the industry.
Key Takeaways
Integrating AI-powered computer vision systems into automotive manufacturing can revolutionize efficiency, quality, and safety across the production line. However, to maximize these benefits, manufacturers must carefully consider essential factors, from camera selection and image processing capabilities to system integration and long-term scalability. This blog explores the critical considerations for implementing computer vision in an automotive environment, detailing the key areas that automotive manufacturers need to address, including camera placement, real-time processing, seamless integration, workforce training, and regulatory compliance.
1. What are the essential factors to consider in selecting and placing cameras for an AI-powered computer vision system in automotive manufacturing?
Selecting and placing cameras for an AI-powered computer vision system in automotive manufacturing requires considering several key factors. These include camera resolution and sensitivity, where high-resolution cameras with excellent sensitivity are necessary for capturing detailed images in the variable lighting conditions common in factories. The field of view and strategic placement are also critical to ensure full coverage of the conveyor belt, so no component is missed during inspection. Additionally, cameras need durability and ease of maintenance to withstand the industrial environment while ensuring minimal downtime for repairs or adjustments.
2. What role does the Image Processing Unit (IPU) play in the computer vision system, and what capabilities must it have to be effective?
The Image Processing Unit (IPU) is central to the computer vision system’s functionality, as it processes the images captured by the cameras to identify and analyze components in real-time. Essential capabilities for the IPU include processing power sufficient to handle high-speed image analysis without causing bottlenecks, which is crucial for maintaining production efficiency. It must also support key computer vision techniques like edge detection, feature matching, and image segmentation, which help recognize shapes, detect defects, and ensure quality. Furthermore, software compatibility with the latest image processing and machine learning tools is vital to keep the system current with updates and upgrades.
Discover how a rapidly growing company achieved $500M revenue in just 12 years, expanding across tech, medical, and aerospace sectors globally by partnering with Lightrains
3. How should the computer vision system integrate with existing manufacturing and data management systems?
For a computer vision system to function optimally, it must have seamless connectivity with existing manufacturing systems, particularly the Manufacturing Execution Systems (MES) and Enterprise Resource Planning (ERP) systems. This connectivity allows for streamlined operations by integrating the AI system’s output directly into the production workflow. Efficient data handling is also essential due to the high volume of data generated, requiring secure storage, rapid retrieval, and robust analysis tools. Effective data management supports real-time decision-making, quality control, and continuous improvement efforts in the manufacturing process.
4. What are the human and organizational factors that influence the successful adoption of the computer vision system?
Human and organizational factors play a significant role in the adoption of AI-powered computer vision systems. Operator training is critical, as staff need to understand how to interact with the system, interpret outputs, and respond appropriately to any alerts or issues identified. Additionally, change management strategies are necessary, as introducing advanced technology often requires a cultural shift within the organization. Ensuring that employees are supported throughout this transition can lead to smoother integration, better acceptance, and enhanced user proficiency with the new technology.
5. How can automotive manufacturers ensure the long-term viability and compliance of the computer vision system?
Automotive manufacturers can ensure long-term viability by focusing on scalability and future-proofing the computer vision system. Scalability ensures the system can grow alongside the production line or adapt to other technological integrations. Future-proofing involves selecting components and software that can be updated without major overhauls, allowing the system to keep pace with technological advances. Regulatory compliance with industry standards, especially concerning safety and data security, is also crucial to avoid legal issues and protect employees. Regular maintenance, reliable technical support, and a clear budget for future upgrades are necessary for sustained performance and adaptability.
This article originally appeared on lightrains.com
Leave a comment
To make a comment, please send an e-mail using the button below. Your e-mail address won't be shared and will be deleted from our records after the comment is published. If you don't want your real name to be credited alongside your comment, please specify the name you would like to use. If you would like your name to link to a specific URL, please share that as well. Thank you.
Comment via email