In late 2023, ClientXYZ (not actual), a rapidly growing manufacturing company operating under strict confidentiality protocols, recognized the need to optimize their conveyor belt systems across multiple facilities. They engaged Lightrains Consulting to reduce costs and errors in their operations. The collaboration began in early 2024.
Challenge
ClientXYZ’s swift expansion had led to inconsistencies in their manufacturing processes, particularly in their conveyor belt systems. These inefficiencies were causing increased downtime, quality control issues, and rising operational costs.
Solution
Lightrains’s team implemented a multi-faceted approach:
- Data analysis: Deployed IoT sensors across all conveyor systems.
- AI-driven maintenance: Implemented predictive maintenance algorithms.
- Staff training: Developed VR-based training programs.
- Quality control: Installed computer vision systems for real-time defect detection.
Results (After 6 months of implementation)
17% reduction in costs and errors
22% improvement in operational efficiency
35% increase in equipment lifespan
15% boost in production output
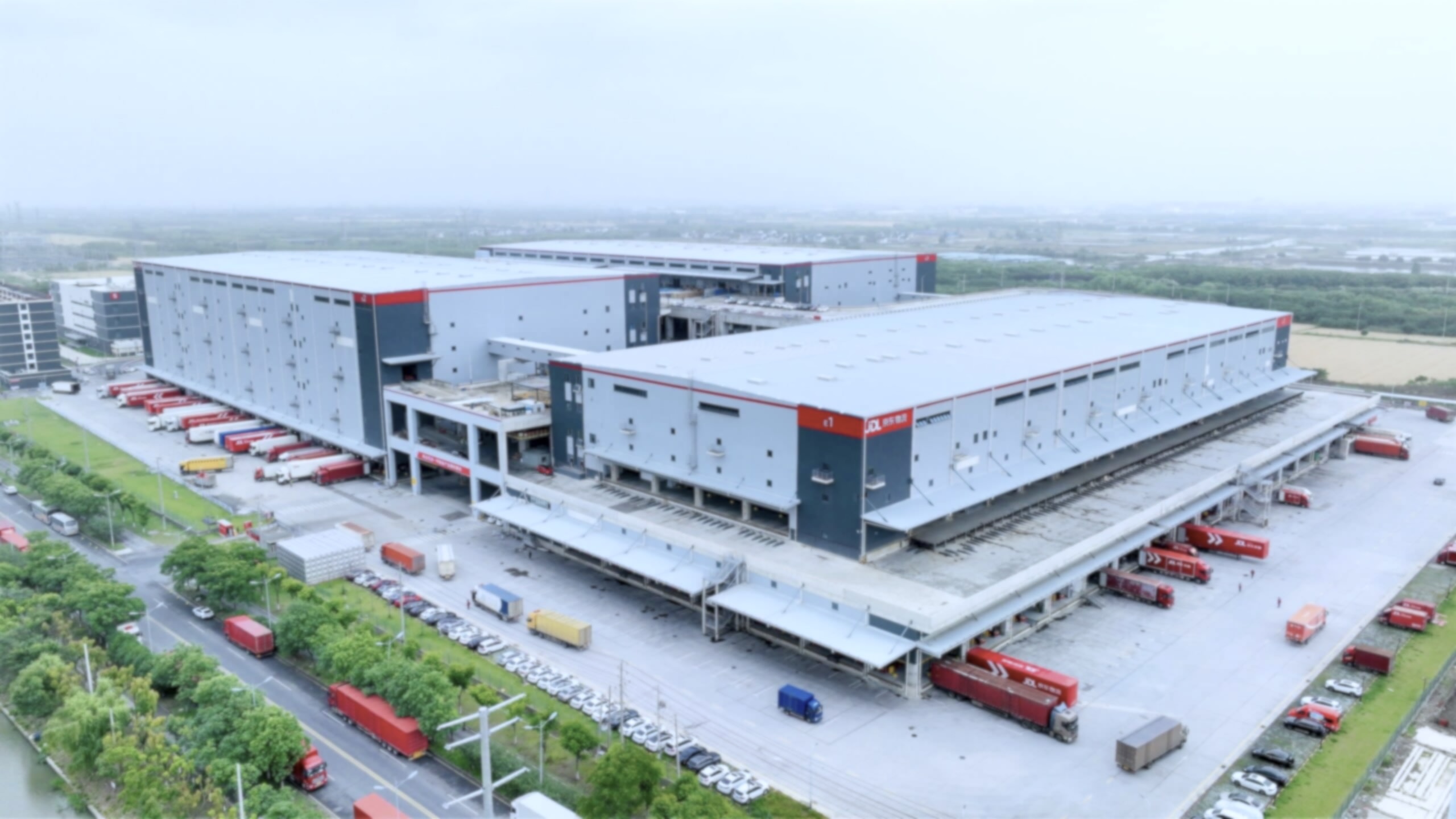
ClientXYZ Company History
2012: Foundation ClientXYZ was established as a small industrial parts manufacturer in Detroit, Michigan. Initial operations involved manual assembly lines for automotive components.
2014: Automotive Expansion Invested $5 million in the first automated conveyor system for a new automotive parts production line. This increased output by 40% and reduced labor costs by 25%.
2016: Consumer Electronics Entry Opened a 100,000 sq ft facility in Austin, Texas, dedicated to consumer electronics assembly. Implemented a state-of-the-art conveyor system with precision control for delicate components, increasing production capacity by 60%.
2018: Food Processing Venture Acquired a struggling food processing plant in California for $30 million. Revamped the entire facility with advanced stainless steel conveyor systems designed for hygiene and efficiency in food handling. This move diversified ClientXYZ’s portfolio and increased revenue by $50 million annually.
2020: Packaging Integration Purchased PackRight Solutions, a packaging company in Georgia, for $75 million. This acquisition added 15 miles of conveyor belts across three facilities, handling everything from small electronics packaging to large appliance boxes.
2022: Automated Warehouse Launch Invested $100 million in a cutting-edge automated warehouse in Pennsylvania. This facility featured multi-level conveyor systems integrated with AI-driven sorting and robotic picking arms, reducing order processing time by 70%.
2024: Lightrains Partnership Facing increasing operational costs and efficiency challenges across its diverse operations, ClientXYZ partnered with Lightrains Consulting. The goal: to optimize conveyor belt systems company-wide, ultimately achieving a 17% reduction in costs and errors.
Present Day
ClientXYZ now operates 12 facilities across the United States, with over 50 miles of conveyor belts in total. Their systems handle a diverse range of products including automotive parts, electronics, food items, and various packaged goods. The company employs over 5,000 people and has an annual revenue exceeding $800 million.
Current challenges include maintaining consistent efficiency across different types of conveyor operations, reducing energy consumption, and integrating IoT sensors for predictive maintenance.
This article originally appeared on lightrains.com